Galileo flow rate sensor comparative performance
Introduction
Microfluidics is a powerful tool to add perfusion to a diverse range of experiments on the microscale. In the biology field, perfusion can turn a static cell culture chamber into a microenvironment with flow to mimic physiological conditions. For example, flow can be modulated to represent vascular flows, interstitial flow or lymphatic drainage.
Applications of adding flow to cell assays are wide and varied such as cell rolling-adhesion, tumor metastasis, molecular transport, metabolism and microphysiological systems (MPS or organ-on-chip). Practical advantages of perfusion include nutrients exchange, medium conditioning, waste removal, and the addition of shear stress as a mechanical stimulus.
Flow setups further enable the automated addition of reagents, collection of samples in real-time for dynamics studies, or the continuous sensing of parameters.
The backbone of a perfusion setup is the pump to move the liquid. A flow rate sensor is a key component that can provide highly complementary flow rate measurement and/or control to perfusion setups. In particular, an inline flow sensor will allow you to measure the flow profile of your pumping system, including measuring the stability and pulsatility of your flow profile or accuracy of your pump.
Our new Galileo flow rate sensor is compatible for use with any pump, including pressure-based pumps, syringe pumps and peristaltic pumps.
The Galileo flow rate sensor is designed with a base and snap-in cartridge format. The flow path is contained entirely within the cartridge that can be swapped to measure different flow rate ranges, or when it is important to avoid cross-contamination between experiments. Our sensor also features a unique clogging alert light to notify the user that the measurement reading is drifting or if the sensor is fully blocked.
This application note compares the performance of our Galileo flow rate sensor to two of the most commonly available flow sensors on the market today, Bronkhorst and Sensirion flow sensors. We use a pressure controller pump for maximum flow stability.
Applications
Applications of the Galileo flow rate sensor in microfluidic cell culture experiments and cell assays are diverse. The following examples are not exhaustive:
- Cell culture under flow
- Microfluidic cell assays (e.g. cell attachment, migration, metastasis)
- Microphysiological systems (MPS, organ-on-chip)
- Molecular transport (e.g. drug toxicity, absorption, filtration, blood-brain-barrier)
- Droplet microfluidics (e.g. cell encapsulation, double emulsions, nanoparticle formation)
- Measure the pulsatility of your flow profile to assess how it affects your cells
- Monitor the accuracy and stability of your pump
Setup
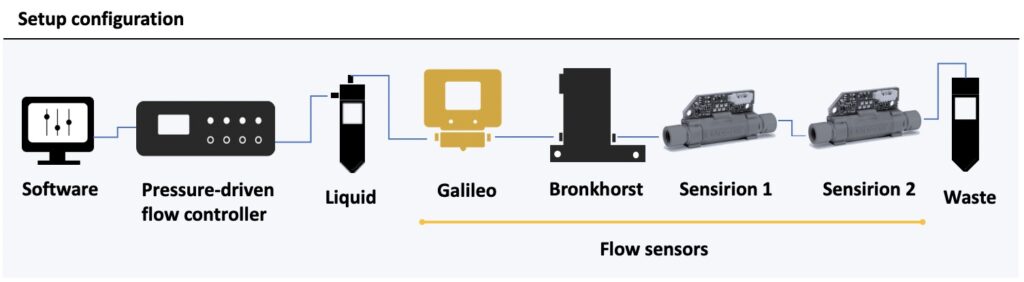
In this setup, a pressure-driven flow controller (OB1 MK4, Elveflow) was used to push the liquid. The Galileo flow rate sensor was connected inline before a Bronkhorst mini CORI-FLOW digital mass flow meter and two Sensirion flow sensors, LG16-0431D (Sensirion 1) and LG16-1000D (Sensirion 2).
Materials
Hardware:
- Flow controller (e.g. pressure-driven OB1 MK4 with one 0-2000 mbar channel, Elveflow)
- Galileo flow rate sensor (6-200 µl/min cartridge used here; Note: other ranges are available)
- Comparison flow sensors, Bronkhorst (1.6 µl/min – 3 ml/min; 0.2% accuracy) and Sensirion (2-80 µl/min, range of 5% accuracy, Sensirion 1; and 40-1000 µl/min, range of 5% accuracy, Sensirion 2)
- Tubings (PTFE, 1/16” outer diameter; OD), fittings and reservoirs
Chemicals:
- Distilled water, filtered
Quick start guide
Instrument connection
1. Connect your OB1 pressure controller to an external pressure supply using pneumatic tubing, and to a computer using a USB cable. For detailed instructions on OB1 pressure controller setup, please read the “OB1 User Guide”.
2. Turn on the OB1 by pressing the power switch.
4. Press Add instrument \ choose OB1 \ set as MK4, set pressure channels if needed, give a name to the instrument and press OK to save changes. Your OB1 should now be on the list of recognized devices.
7. Connect the Galileo flow rate sensor base to your computer with a USB cable.
8. Insert the flow sensor cartridge into the base.
9. Open the Galileo software. (Download the software)
11. OPTIONAL: Connect additional flow rate sensors to the OB1 MK4.
Note: This application note compares the performance of the Galileo flow sensor to other commercially available flow sensors. One flow sensor is normally sufficient for a regular experiment.
Setup preparation
1. Connect the reservoir caps to the OB1 with pneumatic tubing.
2. Connect the reservoir to the Galileo flow sensor cartridge inlet with 1/16” OD tubing.
3. OPTIONAL: Connect a Bronkhorst flow sensor followed by Sensirion flow sensors spanning the desired flow measurement range using 1/16” OD tubing. Here we used a Bronkhorst mini CORI-FLOW digital mass flow meter and Sensirion LG16-0431D and LG16-1000D flow sensors.
Pressure profile configuration
1. Prepare a pressure step profile spanning the measurement range of the flow sensor of interest using the ESI (Elveflow software used to control the OB1; Fig. 1).
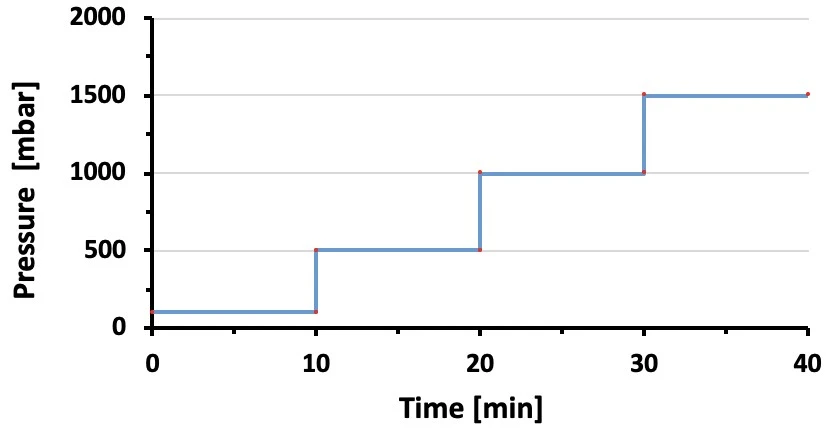
Experiment
1. Start Galileo acquisition on the software interface (acquisition sampling time 0.1 s)
2. Start the pressure sequence.
Results
A series of pressure steps were set spanning a flow range from ~10 – 150 µl/min. Galileo and Sensirion flow rate sensor data were compared to Bronkhorst flow sensor values at each pressure step (Figures 2, 3).
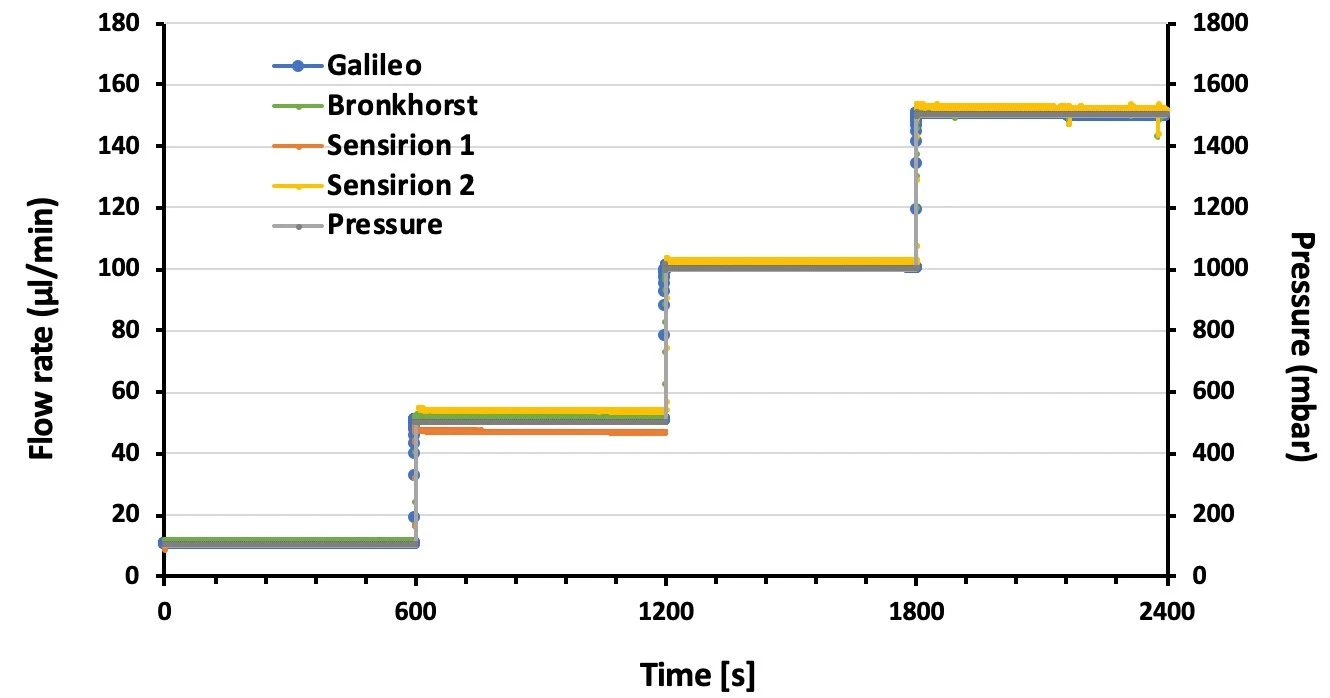
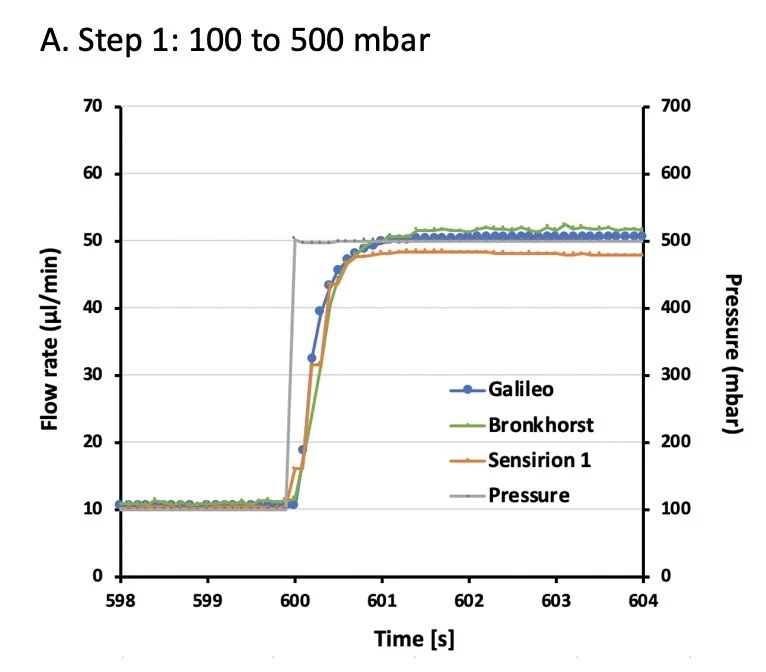
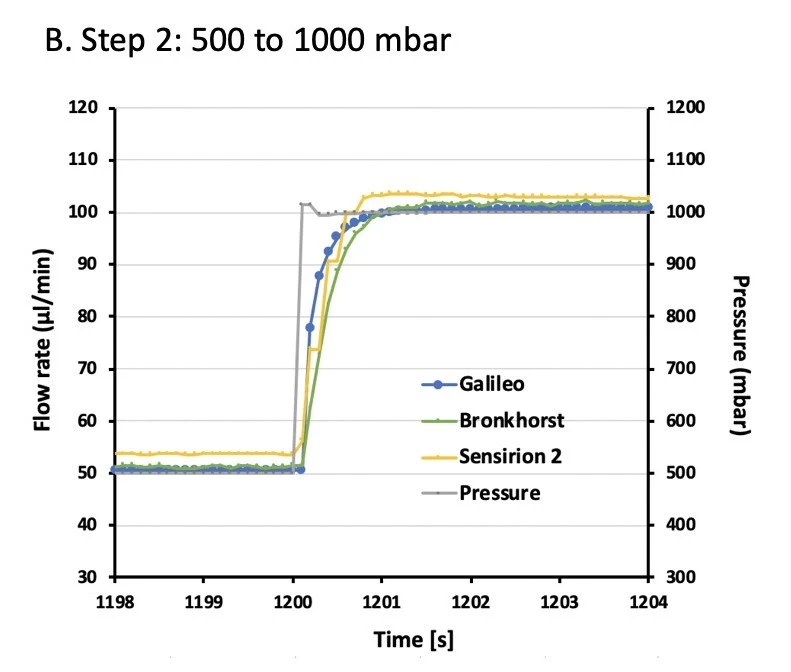
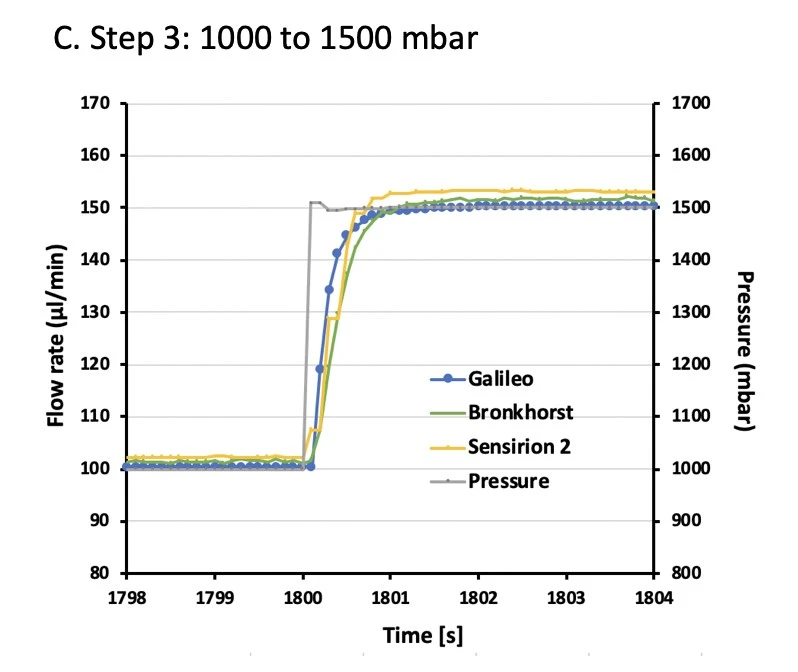
Data were analyzed for accuracy and stability. Accuracy was calculated for each pressure step as the average of 500 s of data (i.e. between 50-550 s of each step). Error is shown as the percent deviation compared to the Bronkhorst flow sensor (Table 1).
Table 1. Accuracy of the Galileo flow rate sensor as a percent error relative to a Bronkhorst flow sensor (reference). Measured Sensirion flow sensor accuracy is also given. Galileo was within 5% accuracy across the whole flow rate range tested (n=3).
Pressure step: 100 mbar | ||||
Sensor name | Galileo | Bronkhorst | Sensirion 1 | Sensirion2 |
Average error % | 3.159 | reference | 4.604 | out of range |
Pressure step: 500 mbar | ||||
Sensor name | Galileo | Bronkhorst | Sensirion 1 | Sensirion 2 |
Average error % | 1.678 | reference | 8.958 | 4.700 |
Pressure step: 1000 mbar | ||||
Sensor name | Galileo | Bronkhorst | Sensirion 1 | Sensirion 2 |
Average error % | 0.799 | reference | out of range | 0.597 |
Pressure step: 1500 mbar | ||||
Sensor name | Galileo | Bronkhorst | Sensirion 1 | Sensirion 2 |
Average error % | 0.593 | reference | out of range | 0.774 |
Stability was calculated as the sample variance (spread) over 100 s of data for each pressure step (i.e. from 400-500 s of each step; Table 2).
Table 2. Average stability of the Galileo flow rate sensor at each pressure step. Measured Bronkhorst and Sensirion flow sensor stability is also given (n=3). Galileo displayed a sample variance of 1-3 orders of magnitude smaller than the other flow sensors.
Pressure step: 100 mbar | ||||
Sensor name | Galileo | Bronkhorst | Sensirion 1 | Sensirion2 |
Average variance | 0.000052 | 0.055690 | 0.000470 | out of range |
Pressure step: 500 mbar | ||||
Sensor name | Galileo | Bronkhorst | Sensirion 1 | Sensirion 2 |
Average variance | 0.000059 | 0.063217 | 0.004844 | 0.010891 |
Pressure step: 1000 mbar | ||||
Sensor name | Galileo | Bronkhorst | Sensirion 1 | Sensirion 2 |
Average variance | 0.00032 | 0.06292 | out of range | 0.01343 |
Pressure step: 1500 mbar | ||||
Sensor name | Galileo | Bronkhorst | Sensirion 1 | Sensirion 2 |
Average variance | 0.0029 | 0.1370 | out of range | 0.1130 |
More tips included in the Application Note PDF!
Acknowledgements
This application note is part of a project that has received funding from the European Union’s Horizon research and innovation program under HORIZON-EIC-2022-TRANSITION-01, grant agreement no. 101113098 (GALILEO).
This application note was written by Lisa Muiznieks, PhD.
Published on July 2024
Contact: Partnership[at]microfluidic.fr
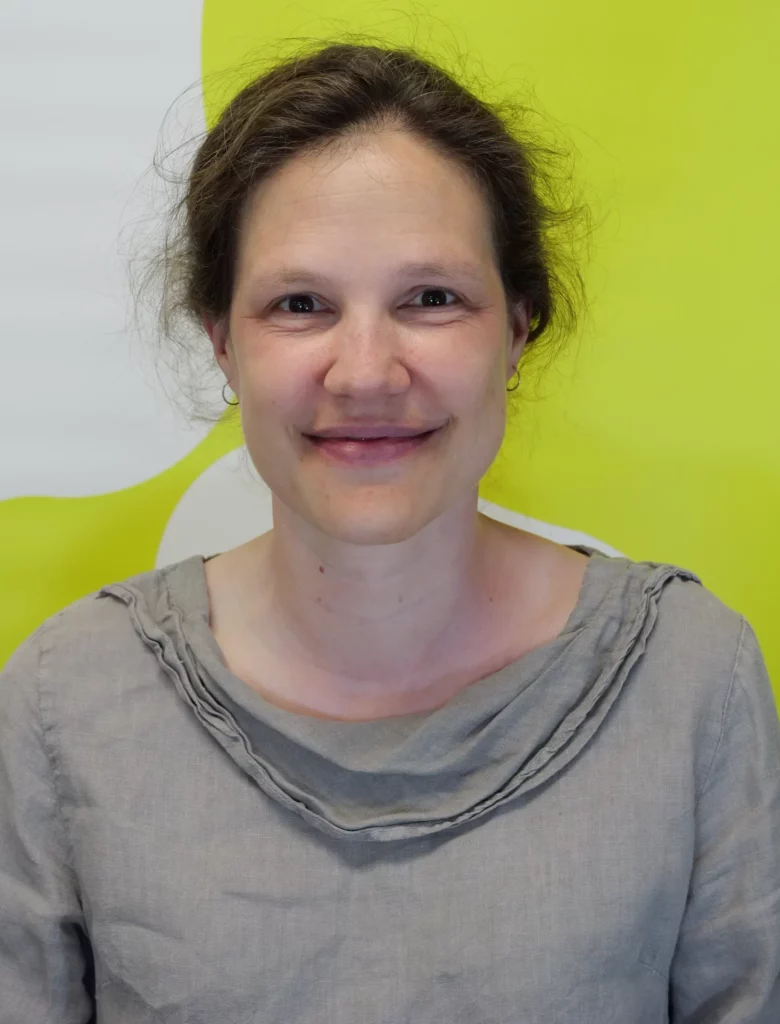