Magnetic fluids and microfluidics: a review
Introduction to magnetic fluids and microfluidics
Magnetic manipulation of micro-fluids is an attractive concept. Due to the non-invasive nature of magnetic fields, magnetic particles or magnetic fluids can be manipulated inside a microfluidic channel by external magnets that are not in direct contact with the fluid.
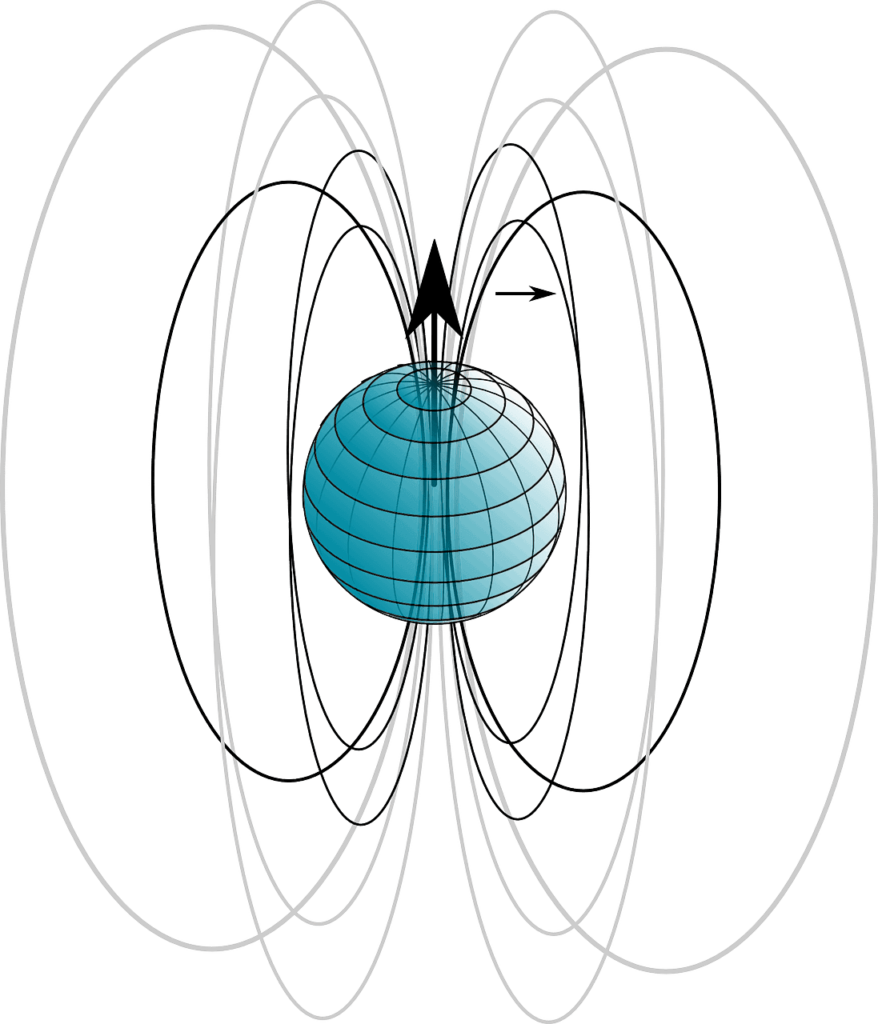
Ferrofluids make up a specific class of magnetic fluids. Ferrofluids are stable colloid suspensions of magnetic nanoparticles in a nonmagnetic carrier fluid, exhibiting both magnetic and fluidic properties.
External magnetic fields can be applied to control their fluid motion, and their fluidic properties are retained even under the influence of strong magnetic fields. Ferrofluids can move just as single component fluids through microchannels of microfluidic devices.
This review will present an overview of the use of ferrofluids in microfluidic devices for pumping, mixing, droplet generation, sorting and separation, valves and seals, and digital microfluidics.
Ferrofluids for microfluidics
A magnetic fluid, or ferrofluid, constitutes particles of magnetic materials such as magnetite, maghemite, or cobalt ferrite dispersed in a base fluid, such as water or organic solvent. The size of the particles is typically 5-20 nm, and the number of particles is in the order of 1023 particles per cubic meter [1].
The ferrofluid behaves as a homogenous continuum if the particles are sufficiently small, about 15 nm or less. This means Brownian motion keeps the particles suspended and does not settle out due to gravity or a magnetic field. The nanoparticles are often coated with a surfactant layer to maintain the spacing between adjacent particles, as they otherwise tend to adhere together due to magnetic forces and van der Waals forces. Ferrofluids must be synthesized as they do not appear in nature.
There are two methods to prepare ferrofluids:
- One-step method: nanoparticles are fabricated in base fluids directly
- Two-step method: nanoparticles are fabricated first, then separated and redispersed in base fluid.
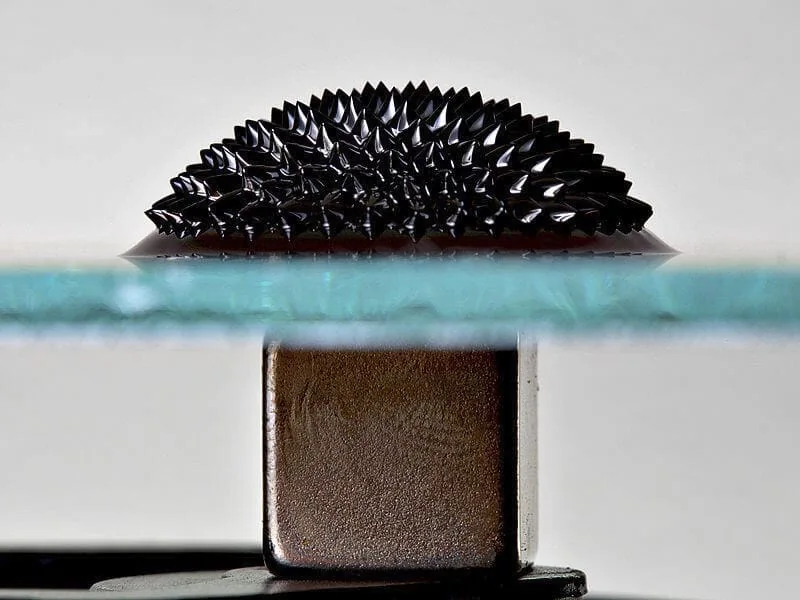
The magnetic particles in a ferrofluid are small enough to contain a single magnetic domain, and the net magnetization is, hence, temperature dependent. Below a critical temperature, referred to as the Curie temperature (TC), the magnetic moments of the ferrofluid are aligned in one direction, resulting in a net magnetization.
The magnetic moments become randomly oriented as the temperature exceeds the Curie temperature, and the ferrofluid loses its net magnetization. An applied thermal gradient thus results in a non-uniform magnetization. The ferrofluid will experience a body force, the Kelvin body force, inducing a fluid flow along the thermal gradient. This thermomagnetic convection can drive the ferrofluid without a pump [2].
Thermomagnetic convection in ferrofluids
Ferrofluids exhibit superparamagnetic properties. Superparamagnetism means that the particles are magnetized when a magnetic field is present. Still, when the magnetic field is removed, they behave like nonmagnetic materials as they have no magnetic memory.
Heat transfer of ferrofluids
The thermal conductivity of magnetic nanoparticles is typically order-of-magnitude higher than the basefluid. The addition of nanoparticles, therefore, remarkably increases the thermal conductivity of the base fluid. This is usually quantitatively demonstrated as a thermal conductivity enhancement or convective heat transfer coefficient enhancement.
Further improvements in the heat transfer coefficient of ferrofluids have been observed when magnetic fields are applied. This is thought to be due to the alignment of magnetic nanoparticles in the direction of the applied magnetic field, forming chainlike structures that provide a heat-conductive pathway [3]. These results have been observed under forced and free convective heat transfer conditions. Ferrofluids have, therefore, been used as heat transfer fluids, e.g., for cooling microdevices [4].
Ferrofluids in microfluidic systems
An external magnetic field acting on ferrofluids in microfluidic devices can be generated by permanent magnets or electromagnets. They can be positioned outside the microfluidic device or integrated into it. Integrated magnets have the advantage of proximity with the fluid, thus requiring lower field strength. However, that requires more complex fabrication steps that may require clean room facilities.
Ferrofluidic pump
Hatch et al. [5] presented a ferrofluidic pump where plugs of ferrofluid were used to pump non-ferrofluids through microchannels. The ferrofluid and the non-ferrofluid must be immiscible. Their device consisted of a circular pump with two ferrofluidic plugs and two external magnets that controlled the movement of the plugs.
One plug was placed between the inlet and the outlet, acting as a closed valve. The other plug was dragged around the circle by a rotating magnet, serving as a piston, pushing and pulling the liquid in and out of the circular channel.
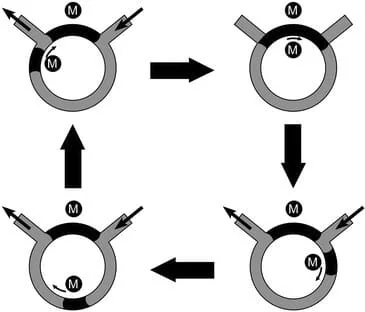
Magnetocaloric pump
As described earlier in this review, the magnetocaloric effect resulting in thermomagnetic convection can be used to pump fluid in a microchip. Love et al. [6] reported a magnetocaloric pump that used only thermal and magnetic fields to drive a microchannel’s fluid flow. They used a ferrofluid plug with low Curie temperature, which was attracted to a region by a magnetic field.
The ferrofluid plug was then subjected to heating; as its temperature approached the Curie temperature, the magnetic attraction of the fluid weakened, and more excellent fluid was then attracted to the magnetic field and displaced the heated fluid. This eventually established a flow, and the pump was used to push non-ferrofluids through the microsystem. The principle is demonstrated in Figure 3.
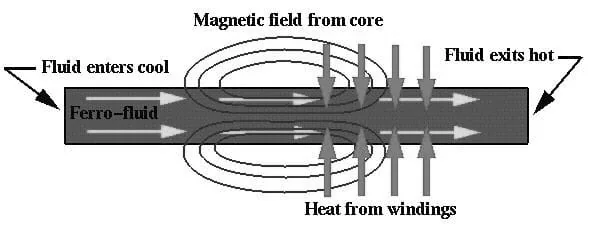
Mixing
Mixing is a critical concept in microfluidics, and rapid mixing is essential for many biological and chemical assays. Several passive and active strategies have been suggested to improve mixing efficiency.
Dynamic mixers generally provide better mixing efficiency than passive ones but usually require more energy and have higher fabrication costs. Another issue with active mixers is the Joule heating that may damage biological samples.
Tsai et al. [7] developed a simple, low-cost y-shaped micromixer to study the mixing between a water-based ferrofluid and water. They placed a permanent magnet below the microchannel and varied the volumetric flow rate and channel width to improve mixing efficiency. They found that the mixing efficiency of ferrofluid and water under the influence of a permanent magnet could reach over 90%, while the mixing efficiency in the same microchannel by only diffusion was consistently below 15%.
This type of magnetic mixer has the advantage of not consuming energy and not producing heat. Other magnetic micromixers have also been suggested, such as microscopic stirrer bars [8], which are rotated by conventional stirrer plates or magnetophoresis of magnetic particles [9].
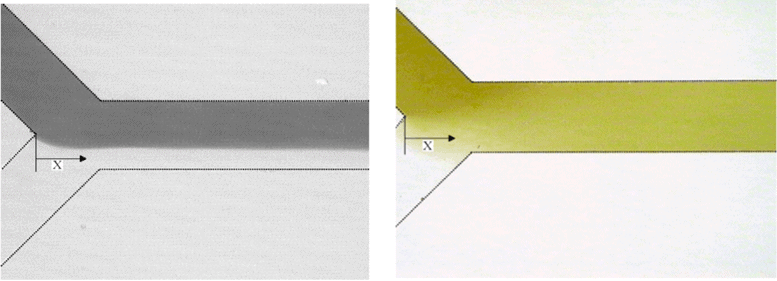
Droplet formation
Ferrofluid droplets can be generated in microfluidic systems by conventional methods of droplet formation at a T-junction or a flow-focusing junction. The ferrofluid droplets can then be manipulated with external magnetic fields in an immiscible fluid or on flat surfaces or substrates.
Tan and Nguyen [10] studied the formation of ferrofluid droplets at a microfluidic T-junction in a magnetic field generated by a small circular permanent magnet. They found that in the absence of a magnetic field, the droplet size varied linearly with the flow rate of the continuous phase.
In a magnetic field, the droplet size could be manipulated with magnetic field strength, the ferrofluid’s magnetization, and the magnet’s position. Placing the magnet upstream of the T-junction led to the formation of more giant droplets as the magnetic force pulled the emerging droplet back, delaying the droplet breakup. Placing the magnet downstream had the opposite effect of accelerating the droplet breakup.
Valves and seals
Hartshorne et al. [11] demonstrated ferrofluidic plugs about 10 mm long as a valve- and seal component in microfluidic devices fabricated in glass. They investigated the performance of ferrofluids as a plug in three different microfluidic configurations: a plug seal in a straight channel, a Y-valve, and a healthy valve.
They used permanent magnets to maneuver the ferrofluids. The valves could open and close well against a low-pressure differential. They observed some loss of small portions of ferrofluid carried downstream with the fluid at higher pressures.
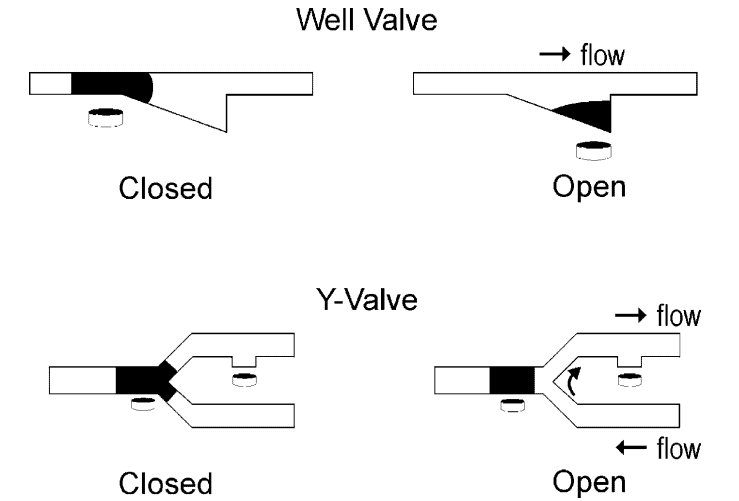
Sorting and separation
Separating target particles from a mixture is crucial in many biological assays.
Magnetic digital microfluidics
In digital microfluidics, fluid droplets can be manipulated on a flat, open surface with no confinements. Discrete droplets can act as individual reaction chambers for chemical or biological reactions or be used to transport reagents. In magnetic digital microfluidics, droplets containing magnetic particles, such as ferrofluids or liquid marbles, are manipulated with permanent magnets or electromagnets.
Nguyen et al. [14] showed that a permanent magnet could deform a sessile ferrofluid droplet, changing its apparent contact angle. The apparent contact angle was seen to decrease with an increasing magnetic field.
They called this phenomenon magnetowetting. The magnet was placed under a planar homogeneous surface. If the magnetic force was strong enough to overcome the resistant friction force and the capillary force, the droplet could slide along a flat surface with the same velocity as the magnet.
However, a general problem with ferrofluidic droplets is that they are not compatible with the environment of the aqueous buffer in many bioanalytical assays [15], as the buffer destabilizes the colloid suspension.
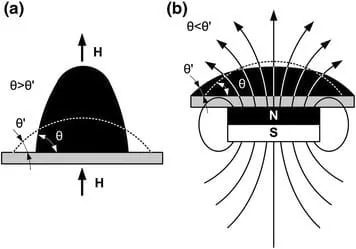
Conclusions and outlook on magnetic fluids and microfluidics
This review presents a selection of works using magnetic fluids in microfluidic systems. Some advantages of magnetic manipulation compared to electric manipulation include controlling both flow and transfer properties (such as heat transfer) and not being influenced by pH, surface charges, or ionic concentration.
However, micro-magnetofluidics remains mainly at a proof-of-concept stage. Several challenges must be overcome before the techniques can be practical. General problems with ferrofluids are the fouling and clogging of microchannels due to the surfactants used to improve the stability of the ferrofluid.
In addition, the nanoscopic properties of ferrofluids are not yet fully understood and must be further studied to exploit their unique properties.
Review done thanks to the support of the MaMi H2020-MSCA-ITN-2017-Action “Innovative Training Networks”
Grant agreement number: 766007
Author: Emma Thomée, PhD
Contact:
Partnership[at]microfluidic.fr
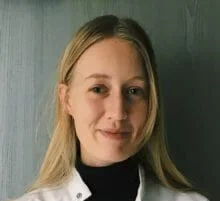
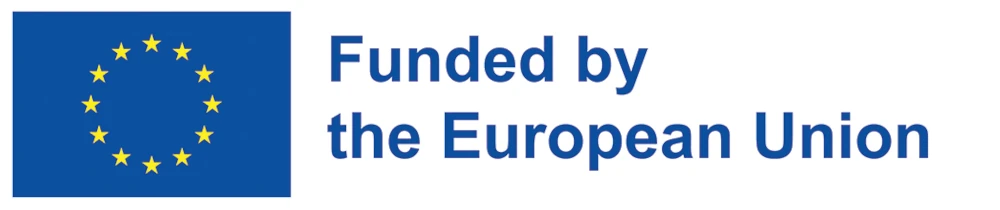
References
- Cowley, M.D., Ferrohydrodynamics. By R. E. ROSENSWEIG. Cambridge University Press, 1985. 344 pp. £45. Journal of Fluid Mechanics, 1989. 200: p. 597-599.
- Singh Mehta, J., et al., Convective Heat Transfer Enhancement Using Ferrofluid: A Review. Journal of Thermal Science and Engineering Applications, 2017. 10 (2): p. 020801-020801-12.
- Azizian, R., et al., Effect of magnetic field on laminar convective heat transfer of magnetite nanofluids. International Journal of Heat and Mass Transfer, 2014. 68: p. 94-109.
- Goharkhah, M. and M. Ashjaee, Effect of an alternating nonuniform magnetic field on ferrofluid flow and heat transfer in a channel. Journal of Magnetism and Magnetic Materials, 2014. 362: p. 80-89.
- Hatch, A., et al., A ferrofluidic magnetic micropump. Journal of Microelectromechanical Systems, 2001. 10 (2): p. 215-221.
- Love, L.J., et al., A magnetocaloric pump for microfluidic applications. IEEE Transactions on NanoBioscience, 2004. 3 (2): p. 101-110.
- Tsai, T.-H., et al., Rapid mixing between ferro-nanofluid and water in a semi-active Y-type micromixer. Sensors and Actuators A: Physical, 2009. 153(2): p. 267-273.
- Yuen, P.K., et al., Microfluidic devices for fluidic circulation and mixing improve hybridization signal intensity on DNA arrays. Lab on a Chip, 2003. 3 (1): p. 46-50.
- Ganguly, R., T. Hahn, and S. Hardt, Magnetophoretic mixing for in situ immunochemical binding on magnetic beads in a microfluidic channel. Microfluidics and Nanofluidics, 2010. 8 (6): p. 739-753.
- Say-Hwa Tan and Nam-Trung Nguyen and Levent Yobas and Tae Goo, K., Formation and manipulation of ferrofluid droplets at a microfluidic T -junction. Journal of Micromechanics and Microengineering, 2010. 20 (4): p. 045004.
- Hartshorne, H., C.J. Backhouse, and W.E. Lee, Ferrofluid-based microchip pump and valve. Sensors and Actuators B: Chemical, 2004. 99 (2): p. 592-600.
- Liang, L., C. Zhang, and X. Xuan, Enhanced separation of magnetic and diamagnetic particles in a dilute ferrofluid. Applied Physics Letters, 2013. 102 (23): p. 234101.
- Jian Zeng and Chen Chen and Pallavi Vedantam and Vincent Brown and Tzuen-Rong, J.T.a.X.X., Three-dimensional magnetic focusing of particles and cells in ferrofluid flow through a straight microchannel. Journal of Micromechanics and Microengineering, 2012. 22 (10): p. 105018.
- Nguyen, N.-T., et al., Magnetowetting and Sliding Motion of a Sessile Ferrofluid Droplet in the Presence of a Permanent Magnet. Langmuir, 2010. 26 (15): p. 12553-12559.
- Zhang, Y. and N.-T. Nguyen, Magnetic Digital Microfluidics – A Review. Vol. 17. 2017.