Oligosaccharide Synthesis
A microfluidic toolkit for precise and automated carbohydrate assembly
Precision flow
Accurate reagent delivery for synthesis
Automated assembly
Simplified chain assembly
Built-in flow monitoring
Real-time flow control with our flow sensor
Optimizing oligosaccharide synthesis with microfluidic flow control
Oligosaccharide synthesis plays a critical role in glycoscience, but researchers often face challenges using traditional batch and syringe-based methods. These methods frequently cause inconsistencies, waste valuable reagents, and offer poor reproducibility, especially during multi-step glycosylation workflows. To reliably assemble complex glycans, you need precise control over reagents, flow, and timing [1].
Our modular microfluidic system, centered around a pressure-driven pump, is engineered to solve these problems through stable flow delivery, programmable pressure control, and on-chip mixing using a meander microfluidic chip. Moreover, to ensure accuracy at every step, the system integrates a microfluidic flow sensor, providing real-time feedback with continuous flow monitoring, thus enabling fine-tuned control of flow rates [2].
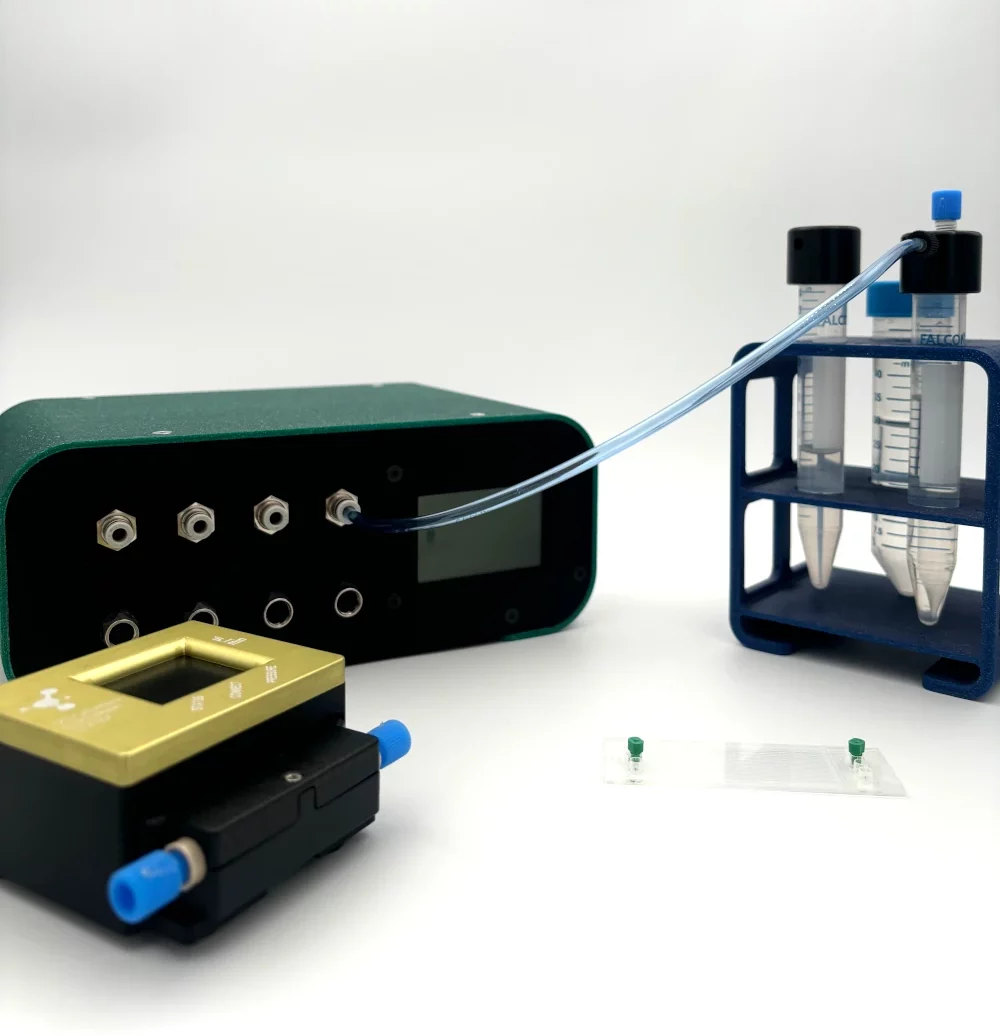
Unlike conventional systems that risk pulsation or mixing atmospheric gas with reagent streams, this setup maintains true input gas and liquid composition, preserving the integrity of your reactions. Consequently, the result is a streamlined platform that supports efficient, reproducible oligosaccharide assembly which is ideal for both chemical and chemoenzymatic workflows [3].
Setup
Pressure pump for microfluidics
Microfluidic flow rate sensor
Meander microfluidic chip glass (eg. Microfluidic ChipShop)
Reservoirs, tubing, connectors
Microscope (optional)
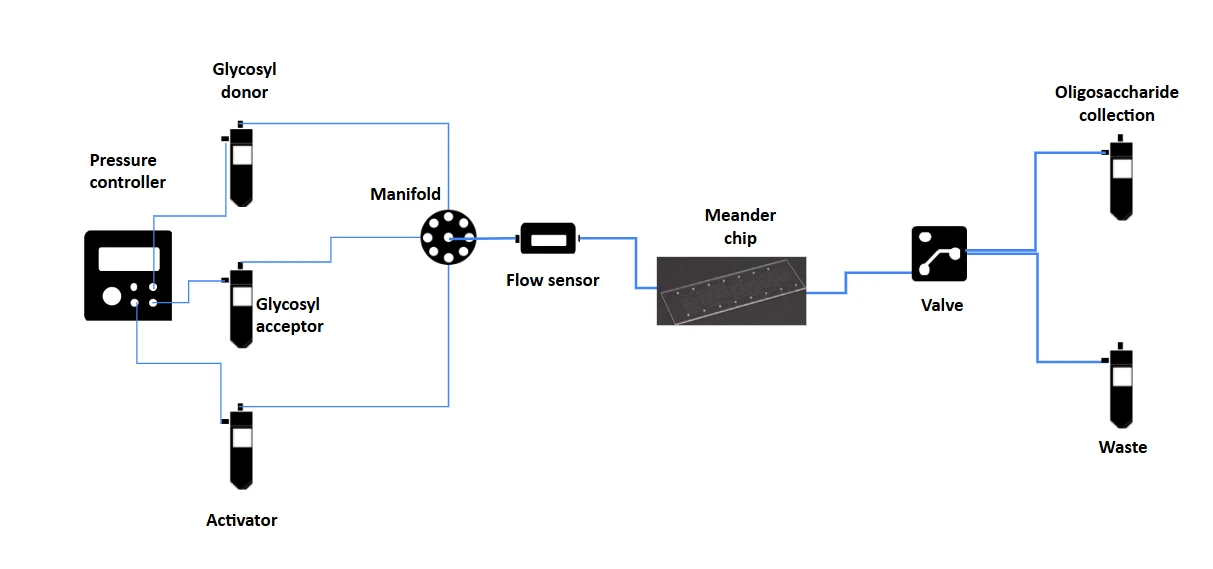
References
Image:
Test tubes descending shades of blue by Minhaa, Wikimedia commons
Text:
Seeberger, P. H., & Werz, D. B. (2007). Automated solid-phase synthesis of oligosaccharides.
Södergren, S., Svensson, K., & Hjort, K. (2021). Microfluidic active pressure and flow stabiliser.
Zhang, Y., et al. (2023). Microfluidics-Based Ionic Catch and Release Oligosaccharide Synthesis.
Oligosaccharide synthesis applications
- Oligosaccharide synthesis and optimization
- continuous-flow glycosylation reactions
- Chemoenzymatic sugar extension
- Automated carbohydrate assembly workflows
- Glycan screening and microarray preparation
Microfluidic flow rate sensor technical specifications
Flow rate ranges: For example, flow rate ranges with <5% accuracy:
0.5 – 60 µL/min
2 – 150 µL/min
40 – 1200 µL/min
0.5 – 10 mL/min
Note that the range can be customized depending on working fluid properties (viscosity, etc.)
Calibrated liquids: aqueous media (others are possible upon request)
Wetted materials: PEEK, steel, fluorosilicone, perfluoropolyether resin
Internal volume: approx. 40 µL (variable depending on the used configuration range)
Operation pressure: up to 3 bar gauge pressure
Maximum pressure rating: up to 6 bar gauge pressure
Software operability: standalone GUI for data visualization and logging; optional Python API
Please note that this is a beta version of this technology, so exact specifications are subject to change.
Microfluidic pressure pump technical specifications
The microfluidic pressure pump can come with 1 to 4 channels. Each channel connects to a flow sensor with a feedback-loop between pressure and flow rate. Each channel has the following specifications (tested with a set pressure value of 2 bar):
Pressure control | |
---|---|
Accuracy | +/- 2.5 mbar |
Air consumption | few ml/min |
Response time | 140 ms |
Settling time | 2750 ms |
Overshoot | 0.12 mbar |
Customize your pack
Our instruments are compatible with standard commercialized chips from different brands.
Our instruments can be added to different setups depending on your specific needs. In this light, our microfluidic specialists will advise you on the best instruments and accessories depending on your needs and will accompany you during the system’s setup.
Frequently asked questions
Can the pressure pump be integrated with existing lab equipment?
Yes, the pump is designed for easy integration with microfluidic setups, chemical reactors, and gas mixing systems.
Can the flow sensor’s cartridges be reused?
Yes, depending on the experiment. The flow sensor cartridges can be reused if there’s no alert of clogging, or if you face no problems of cross-contamination in your experiment.
Do I need a microscope?
Not required, but useful for chip visualization or troubleshooting.
How can we help your experiment?
This pack is in beta testing phase. So, although the instruments are not fully industrialized, we can provide extensive support as part of our beta testing program. Get in touch to see if you are eligible.
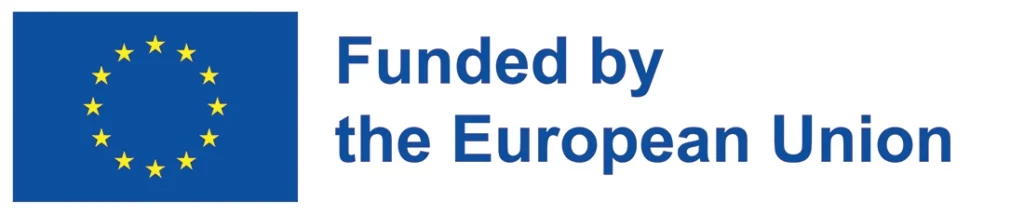
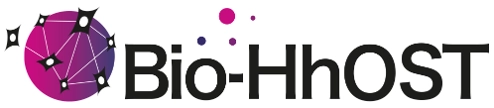
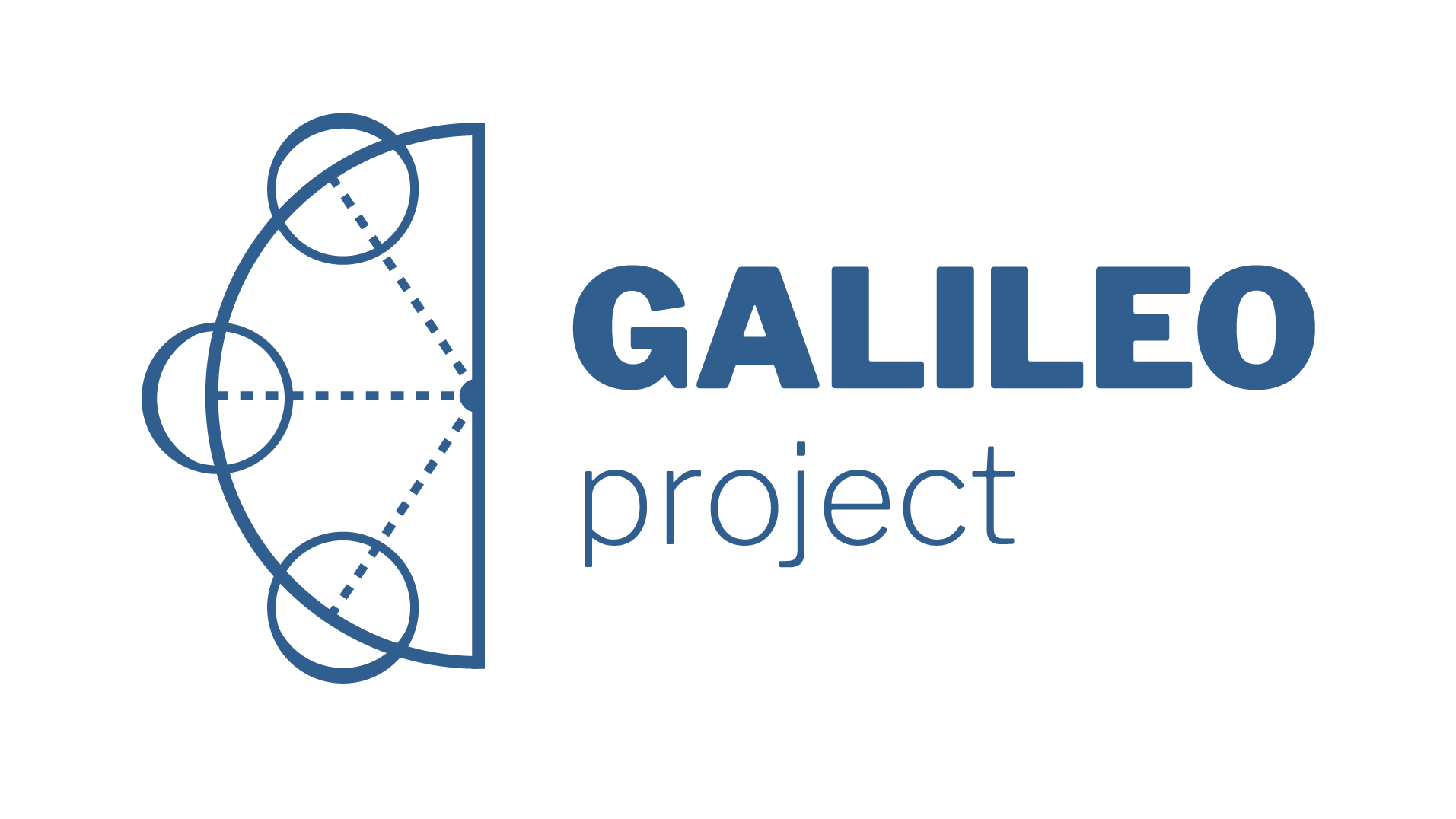