Polystyrene (PS) Molding Microfluidics Setup
Fabricate Polystyrene chips in only 1 hour
The whole microfabrication process is performed outside of a clean room
Easily molded into various shapes and sizes
PDMS chip microfabrication
PDMS is the most commonly used material for the fabrication of microfluidic devices.
In our molding setup, the microfabrication of PDMS chips is performed outside of a clean room and begins by blending PDMS with a curing agent and degassing inside a desiccator. Then, the elastomer is carefully poured onto the mold and undergoes curing in a conventional oven. After completion, the chips undergo demolding and precise cutting, while inlet perforations are made using biopsy punchers. Finally, the PDMS is securely attached to a glass slide following treatment in a plasma cleaner.
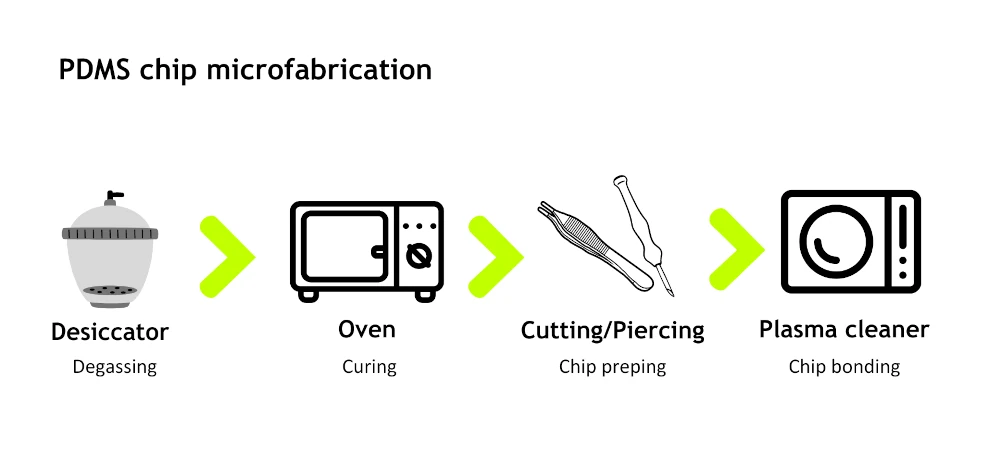
However, PDMS limited chemical compatibility, high gas permeability, and low throughput are reasons why researchers started looking for replacement materials, such as thermoplastics.
Switching to Polystyrene (PS) molding
Consequently, our team of engineers and researchers turned the PDMS microfabrication process into a thermoplastic molding setup for microfluidic chip fabrication. Particularly, they developed the Polystyrene (PS) molding setup.
Polystyrene (PS) is a particularly interesting thermoplastic for chip microfabrication due to its many advantages. It’s an inert, rigid, biocompatible, and commercially available material adapted for mass manufacturing. Its low production costs present a cost-effective option for various applications. Moreover, transparent grades of PS are available, making it suitable for applications where visibility is important. Furthermore, PS material can be easily molded into various shapes and sizes, offering versatility in design and applications.
Microfabrication of Polystyrene follows the same steps as for the thermoplastic chip microfabrication, and both can be performed outside of a clean room.
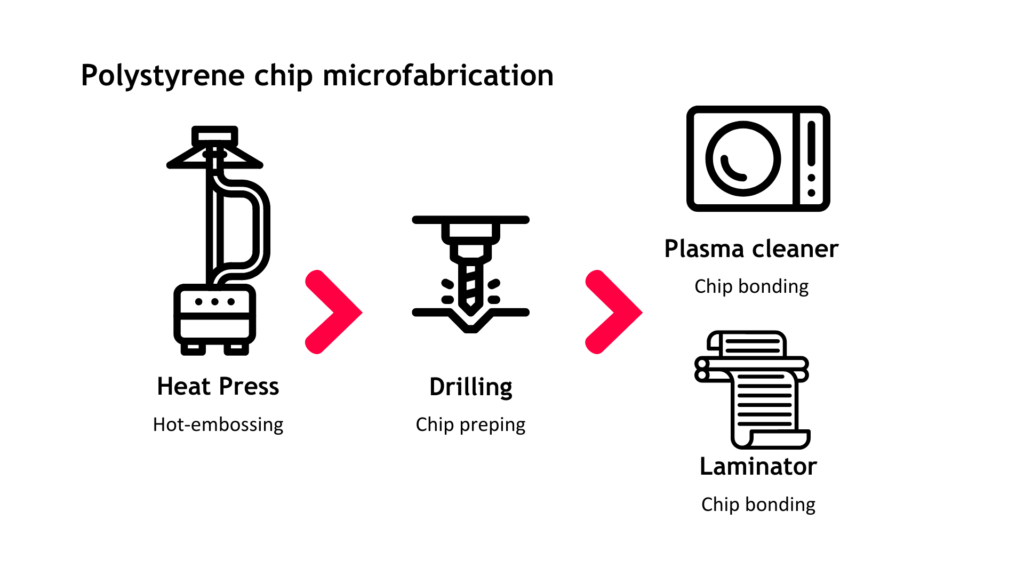
In our polystyrene molding microfluidic setup, we streamline the initial time-consuming phase by implementing a significantly faster hot-embossing process. Subsequently, chip preparation is simplified using drilling tools. Using the existing plasma cleaner and adding a laminator, the chip is sealed.
By integrating our recommended heat press and laminator into your workflow and adhering to our guidelines, you can seamlessly transition from PDMS microfabrication to PS material molding setup.
Your PDMS microfabrication process is different, and you don’t have all the listed equipment? Don’t worry; we’ve got you covered! We can provide you with all the necessary pieces and consumables; just drop us a line!
Technical specifications
The polystyrene (PS) molding microfluidic setup comprises:
Heat press with double heating plate
- Dimensions: 420*550*680mm.
- Max temperature: 300 °C.
- Pressure range: 0-25 tons.
Laminator
- Dimensions: 270*545*130 mm (L x w x h)
- Max. laminated width: 335 mm
- Max. laminated thickness: 35 mm
- Max temperature: 140 °C.
Options: Drilling machine
Consumables: Polystyrene sheets.
Compatibility and Applications
The PS molding setup can also be used with:
- PMMA
- COC/COP
- Polycarbonate
Microfluidic chips produced with PS molding can be employed in:
- Lab-on-a-chip applications, such as nanomaterial synthesis
- Cell culture experiments, such as organ-on-a-chip, gut-on-a-chip
- Applications requiring specific-chip design and chemical inertia
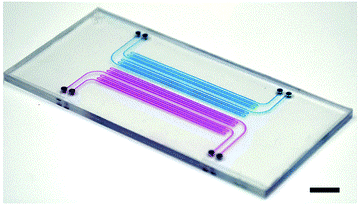
Does the process also involve mold fabrication?
Currently, the polystyrene (PS) molding microfluidic setup focuses on the chip fabrication and bonding from a pre-existing mold. However, we do have expertise to advise you in how to make your own molds.
What is the resolution of the Polystyrene microfluidic devices?
Resolutions as low as 15 µm (channel width) for an aspect ratio of 2:1 can be achieved.
What maximum pressure can the devices withstand?
Based on internal testing, up to 3.5 bar.
What material can I use to close the chip?
The chip can be closed with a thermoplastic slide, a microscope glass slide or a microscopy-compatible polymer slide.
Is this process compatible with microscopy/reversed microscopy?
Polystyrene is optically transparent and well-adapted to microscopy.
Funding and Support
The BIOPROS and MICRO4NANO projects results helped develop this instrument pack, with funding from the European Union’s Horizon research and innovation program under HORIZON-CL4-2021-DIGITAL-EMERGING-01-27, grant agreement no. 101070120 and the European Union under H2020-MSCA-RISE-2020, grant agreement No. 101007804.
Special thanks to Micaela Fernandes and Widad Mesbahi, who largely contributed to the development of this pack.