PMMA DEVICE STATION
A quick way to produce PMMA chips in less than a day
Everything you need to fabricate a versatile and biocompatible microfluidic device
Rapid and customized installation
Advantages
- Fast fabrication process to develop your chip in 5 hours or less.
- Fabricate your high-resolution devices without initial knowledge of microfabrication.
- Highly reproducible processes from reusable molds to PMMA chip fabrication.
- Get advantage of our expertise in photolithography and the hot embossing process.
- Inexpensive and innovative process suitable for different applications.
PMMA devices present properties that convey multiple advantages such as:
Characteristics |
PMMA |
PDMS |
Transparency | Transparent and optically clear | Transparent and optically clear |
Fabrication | Machining, laser cutting | Soft lithography |
Bonding | Solvent bonding, thermal bonding, or adhesive bonding | Oxygen plasma treatment or adhesive bonding |
Elasticity | Rigid | Flexible and elastomeric |
UV radiation resistivity | Moderate to high | Low |
Surface properties | Hydrophobic, requires surface modification for hydrophilicity | Hydrophobic, naturally hydrophilic, can be surface modified |
Gas permeability | Low | High |
Chemical compatibility | Chemically resistant to many solvents and reagents | Limited chemical compatibility, can swell or leach components |
Biocompatibility | Biocompatible with specific cell types and assays | Biocompatible with a wide range of biological samples |
Connection options | External connectors (stainless, steel, plastic) | Tubing or syringe needles |
Connector compatibility & ease of connection | Compatible with a variety of connector types: Requires proper alignment and connection of external connectors | Compatible with tubing or syringe needles: Tubing or needles can be easily inserted into the PDMS channels |
Overall, if you want to do easy prototyping and work at low pressure, PDMS devices are a good fit for your requirements.
If you want to apply high pressure or potentially scale up your process later, PMMA must be the perfect material.
Depending on your final application, our experts help you define the best material to reach your goal.
This pack guarantees a total and autonomous PMMA device manufacturing for microfluidics, Bio-MEMS, or other applications.
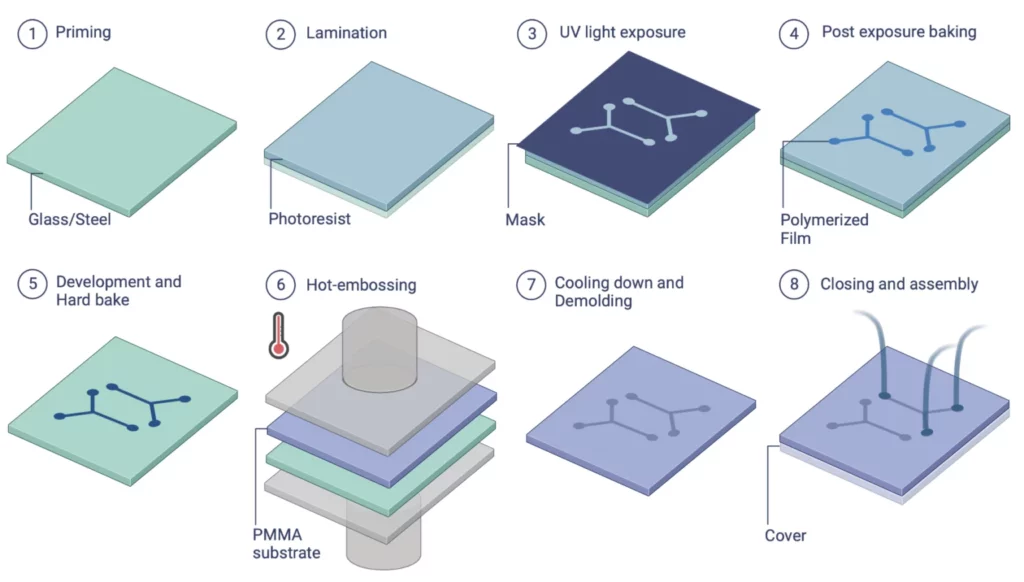
PMMA device station setup
The PMMA device station includes the following:
Master mold fabrication (same as PDMS):
- Laminator
- UV lamp
- Heat plate
PMMA replication:
- Ultrasonic bath
- Heat press
- Oven
- Pressurized air installation
- Plasma cleaner
Materials:
All resources (PMMA film, dry photoresist film) are included. We also provide all product references needed to refill your stock in the future.
Accessories:
All lab accessories (glass slides, iron slides, slide holders, Petri dishes, tweezers, solvent bottles, thermal gloves, etc.) can be included. We also provide all product references needed to refill your stock in the future. The mask used depends on the application. Therefore, a mask design can be discussed.
Chemicals:
All chemicals (Isopropanol, acetone, developer, etc) can be included. We also provide all product references needed to refill your stock in the future.
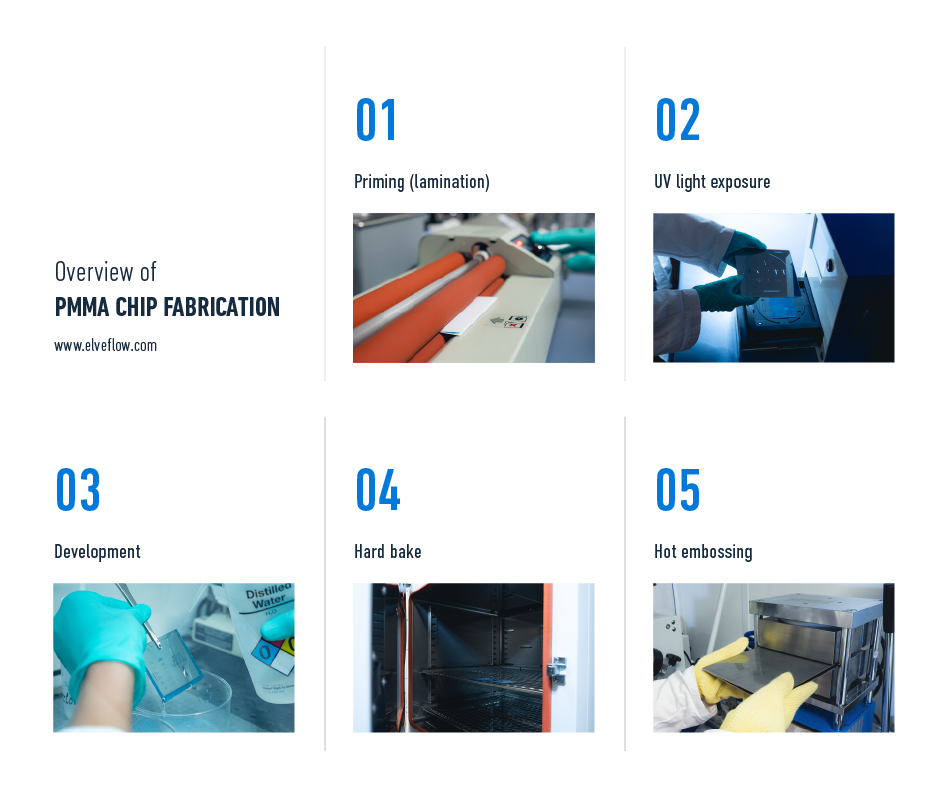
We can also provide:
- Ultrasonic bath
- Drilling machine
- Classical designs of photomasks
Technical specifications
Content
Laminator: An easy-to-use hot and cold laminator
- Dimensions : 500*200*100mm.
- Laminating Speed: 560mm/min
- MAX Laminating thickness: 1mm
UV lamp: A functional exposure-masking chamber operating with a cold UV source with pattern resolutions down to 1µm.
- Dimensions : 260*260*260mm.
- Wavelength: 365nm +/- 5 nm
- MAX Substrate thickness: 2 mm
Heat plate: A programmable hot plate with a smooth temperature ramp.
- Dimensions:203*203 mm.
- Max temperature: 450℃.
- Temperature accuracy: 1%.
Heat press with double heating plate:
- Dimensions:420*550*680mm.
- Max temperature: 300℃.
- Pressure range: 0-25 tons.
Oven: A conventional laboratory oven
- Dimensions: 150 L
- Max temperature: 250°C
Optional
- Ultrasonic bath
- Drilling machine
PMMA device applications
Thanks to its properties (transparency, recyclability, high biocompatibility), the PMMA device can be used for multiple applications such as:
- Biomedical research and diagnostics: Thanks to its transparency that facilitates imagining, PMMA devices can be used for cell culturing, drug screening, DNA analysis, protein assays, and point-of-care diagnostics.
- Droplet-based microfluidics: PMMA devices can generate and manipulate droplets in high-throughput screening, single-cell analysis, and chemical synthesis. PMMA’s compatibility with various fluids and its hydrophobic nature allows for precise droplet generation and control.
- Organ-on-a-chip: PMMA’s transparency facilitates real-time observation and analysis of organ-on-a-chip models.
- Environmental monitoring: such as water quality analysis and pollutant detection. PMMA devices can integrate sensors and detection methods to analyze samples and provide rapid and portable testing solutions.
- Microreactors: PMMA devices can be used as microreactors for chemical reactions at the microscale. These microreactors enable precise control of reaction conditions, enhanced mixing, and reduced reaction times. PMMA’s chemical resistance and ease of fabrication make it suitable for creating microreactor systems.
Overall, PMMA is a well-known material for mass production and, therefore, very easy to manufacture on a large scale. Thus, if you want to go through a prototyping phase for all these applications before possibly considering more significant production, it must be a suitable material for your requirements!
Our team of experts can assist you in determining the most appropriate material based on your final application, ensuring that you achieve your desired outcome.
Customize your pack
Our Packs can be modified depending on your specific needs. Our microfluidic specialists will advise you to provide the best instruments and accessories, depending on your needs. They will accompany you during the setup of the microfluidic platform.
– Check our other Packs for various applications –
Can I order a pack?
Our Packs, such as the Live Cell Imaging pack, are available under specific conditions. As these packs are still in the developmental stage, we have some eligibility criteria to ensure their optimal success rate.
At the Microfluidics Innovation Center, we tailor our approach to suit each researcher’s unique needs. Therefore, before purchasing a Pack, we encourage you to contact our technical team for a detailed discussion of your research objectives and requirements.
To learn more about our Packs or to schedule a consultation with our experts, please contact us at innovation@microfluidic.fr. We look forward to collaborating with you and supporting your research endeavors.
Can I buy individual instruments?
You can order our instruments on the product section of our website.
Funding and Support
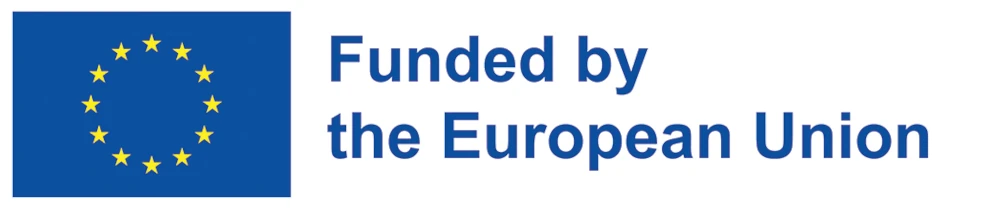
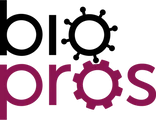
